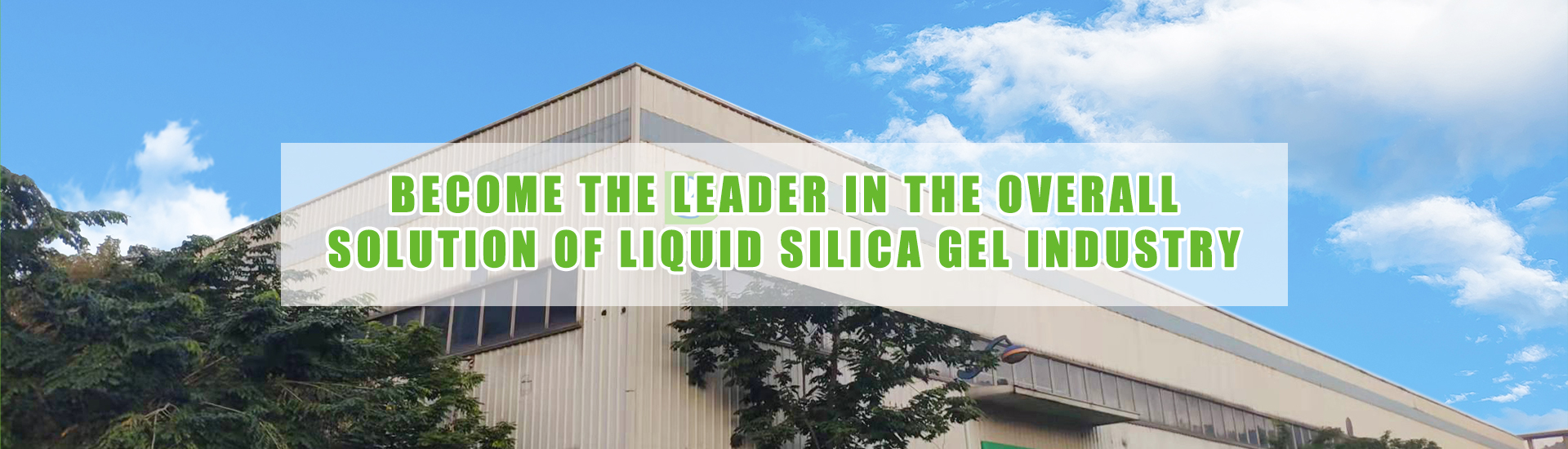
1. Characteristics of two-color/two-material injection molds.
Two-color mold: Two plastic materials are injected on the same injection molding machine, and are molded in two times, but the product is only released once. Generally, this molding process is also called double-material injection molding, which is usually completed by a set of molds and requires a special two-color injection molding machine. Mainly have the following characteristics:
The moving mold is the same, the injection molding process is rotating and needs to be exchanged, so it must be exactly the same. (There are special cases, the cavity may be different during molding)
After the injection of the first runner of the mold is completed, it cannot be left on the mold. Preferably a hot runner, otherwise it can also be grasped by a robot. Worst of all is the latent gate, which can automatically fall off, otherwise the second shot with the gate on top cannot close the mold.
The product is shot twice. After the product is opened, the first shot must remain on the movable mold side. Generally speaking, the products with two shots are generally chosen to stay on the movable die side. Therefore, the mold requires opening and closing devices and tie rods to achieve sequential mold opening. First, open the mold side and add an ejector mechanism on the mold side.
In principle, the two sets of cooling systems require that the temperature of the first shot material is 60 degrees higher than that of the second shot, and the mold temperature of the mold is different, so two sets of cooling systems are required.
2. Brief introduction of two-color/two-material injection process.
Rotary core injection molding process:
During the molding process, the first part is injected in cavity 1 with one resin, then the mold is rotated 180°, the first part to the second large cavity 2 are injected in cavity 1, and another resin is injected into the part ; At the same time, the first part of the second product is injected in the cavity, and the cycle is repeated.
Third, the process characteristics.
At present, two-color molds are becoming more and more popular in the market. This process can make the appearance of the product more beautiful, it is easy to change the color, and does not need to be sprayed, but the cost is expensive and the technical requirements are high.
(1) The two shapes of the female mold are different and form a product respectively, while the two shapes of the male mold are exactly the same.
(2) The front and rear molds of the mold must be matched after rotating 180 degrees in the center. The inspection action must be carried out in the design process, and the mold base positioning and processing requirements are relatively high.
(3) The total thickness of the front formwork plus A plate shall not be less than 170mm. Please carefully check other reference data of this type of injection molding machine, such as the maximum die thickness, minimum die thickness, KO hole distance, etc.
(4) The nozzle of the three-plate mold should be designed for automatic demoulding action, and special attention should be paid to whether the demoulding action of the soft glue nozzle is feasible.
(5) When designing the master mold for the second injection, in order to prevent the glue position of the first molding product from being scratched by the second master mold, a part of the void can be designed. However, we must carefully consider the strength of each sealing position, that is, during the injection molding process, whether the plastic will be deformed under the larger injection pressure, resulting in the possibility of a sharp edge in the second injection.
(6) During injection molding, the size of the product injected in the first injection can be slightly larger, so that it can be pressed more tightly with another male mold during the second injection, so as to achieve the effect of sealing.
(7) Note: During the second injection, will the flow of plastic impinge on the first-molded product, causing its glue position to be deformed. If possible, we must find ways to improve.
(8) Before the A and B plates are closed, pay attention to whether the front mold slider or the inclined top will reset and crush the product first. In this way, it is necessary to find a way to reset the slider or the inclined top of the front mold after the A and B plates are closed.
(9) The water transport arrangement of the two female molds and the male molds is as balanced as possible.
(10) In 99% of cases, the hard part of the product is injected first, and then the soft part of the product is injected, because the soft part is easily deformed.