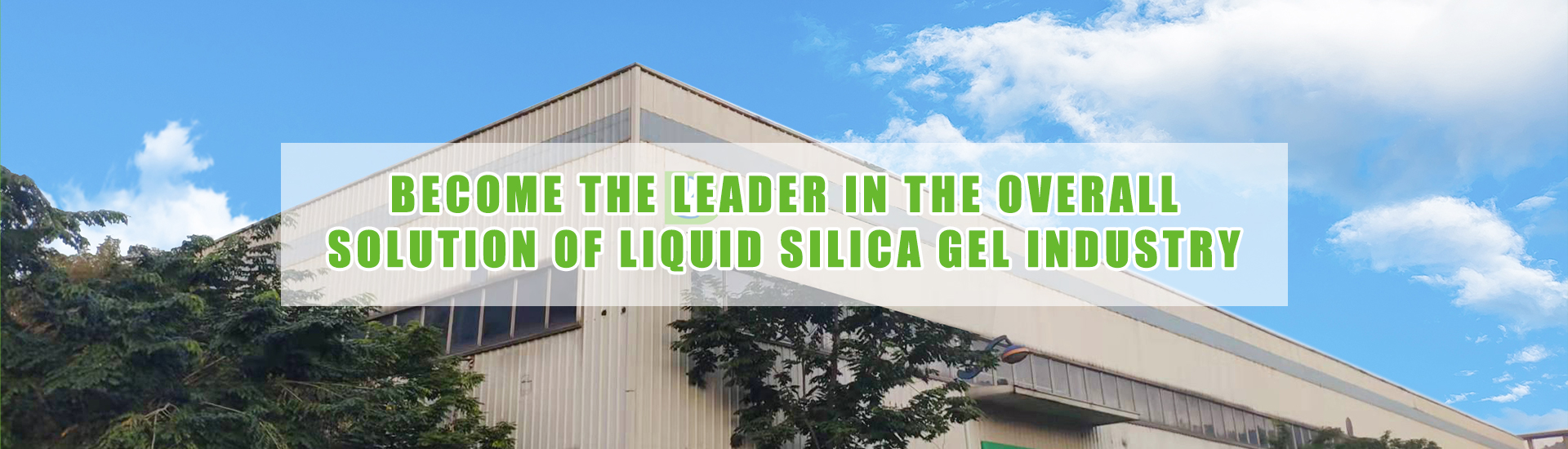
Liquid Silicone Rubber (LSR) is a non-toxic, heat-resistant, flexible thermosetting material with high recovery rate. Its rheological behavior is mainly characterized by low viscosity, fast curing, shear thinning, and high thermal expansion coefficient.
LSR is divided into A glue and B glue. The ratio of 1:1 is controlled by a quantitative device, and then fully mixed by a silicone injection molding machine (Staticmixer), injected into the injection tube, and then injection molded for production. The liquid silicone enters the hot casting mold to produce silicone The product can realize the advantages of one-time molding, no waste, automation and so on.
LSR is widely used in the manufacture of sealed infusion systems, ring dialysis filters, hearing aid components, baby pacifiers, breast shields, home appliance suction valves, medical device components and other medical and health industries.
Its products have good thermal stability, cold resistance, excellent electrical insulation performance, good elasticity, waterproof and moisture resistance, acid and alkali resistance and other chemical substances will not produce toxic substances when burned.
molding process
LSR is a two-component liquid material, divided into A component and B component. The mixer works to thoroughly mix the A and B components in a precise 1:1 ratio. Since some products are colored designs, they are equipped with color pump sets and color measurement sections. A+B components. additive. The colors are fully mixed and then enter the plasticizing system.
The plasticizing screw has the function of homogenization and mixing. The mixture is injected into the hot mold through the screw, and the silica gel is cured at the mold temperature of 170~200℃. When using a cold runner system, it is worth noting that the runner should be sufficiently cold. To avoid glue leakage, the needle valve is installed on the surface of the mold part, and the needle valve closes the nozzle immediately.
1. Feed system.
The following forms can be selected:
1) Bidirectional pump
Since the A.B pumps are connected and synchronized, the feed can be moved up and down to maintain pressure.
Hydro-pneumatic control, so this form of feeding system is more reliable and accurate.
2) One-way pump
General type, only single item feeding.
3) Synchronous single-phase pump with check valve.
4) Measuring cylinder system.
Mainly used for single-phase pumps.
2. The key components of liquid silicone rubber injection molding machine.
1) Due to the low viscosity of LSR, the backflow and glue leakage of the material must be considered during processing, so the screw must be sealed.
2) Needle valve nozzle should be used to prevent LSR from curing.
3) Mixing of A.B components. Measure parts.
3. Mold design.
In mold design, there are generally the following forms:
1) Hot runner
Material waste, simple design, low cost, mostly used for large products.
2) Cold runner with needle valve.
It can be automated and the cycle is short.
3) No needle valve cold runner.
Due to the high coefficient of expansion of LSR, it expands during heating, but shrinks slightly during cooling, so the part cannot maintain an accurate side distance in the mold. Therefore, cold runners can be machined. The LSR should keep the temperature and fluidity low. The cold runner adopts a closed system. During the injection cycle, the closed system employs a sealed needle or needle valve for accurate measurement of the LSR material in the flow channel. Silicone rubber has obvious heating expansion characteristics, the shrinkage rate is 2%~4% (vulcanization temperature is 150℃), and silicone rubber has the characteristics of compression deformation.
Therefore, the design of the mold should pay attention to the following aspects:
1) Use a small injection port to avoid turbulence and jetting;
2) Use needle-shaped or wing-shaped injection ports;
3) Use T-shaped guide bolts instead of cylindrical guide bolts, and use an injection air gun to add heat insulation layers/boards when demoulding;
4) Do not use rust inhibitor/oil containing polymerization inhibitor, generally toluene, xylene, etc. can be used.
Analysis of LSR vulcanization.
1) The sulfur chemical reaction of liquid silicone rubber requires a certain reaction time;
2) Ideal flow, with a diameter of 2mm and a flow distance of more than 170cm;
3) The minimum thickness is 1/1000mm;
4) Excessive mold temperature will lead to vulcanization and hinder flow;
5) Laminar flow can avoid air bubbles;
6) High-speed injection will cause turbulent flow;
7) The viscosity of the material will change the flow pattern;
8) Turbulence causes white spots.